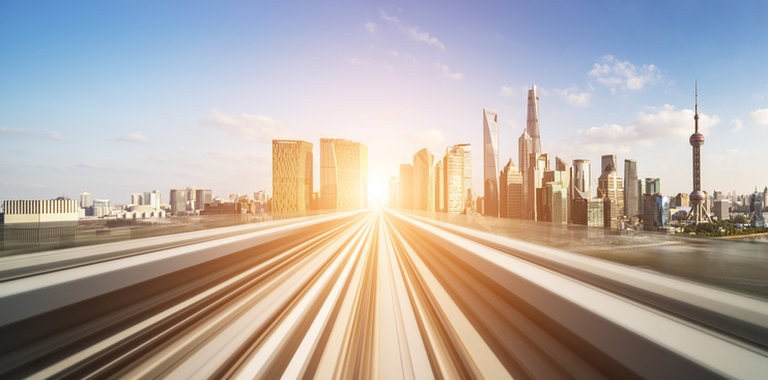
Braking systems manufacturer turns to Druck for high-speed train solutions
Customer Type: Manufacturer of braking systems for high-speed trains
Industry: Railway
Application: Monitoring pressure in brake control units employed on high-speed trains
Solution: Druck's UNIK5000 Pressure Sensing Platform
Based in China, Druck’s customer develops and manufactures braking systems for high-speed trains.
One high-speed train has 8 carriages with 6 to 8 pressure sensors installed in the brake control unit on each carriage. The trains have top speeds of 350km/h and traverse the entire length and breadth of China, where climatic conditions (especially levels of temperature and humidity) vary greatly. Whilst the train is in motion, very high levels of vibration are experienced by the undercarriage which includes the train braking systems. Measuring compressed air pressure of the braking system accurately is critical to the safety and to the comfort of its onboard passengers when slowing the train down from its blistering high speed.
Failure of any sensor in the braking system may cause danger to passengers’ safety, meaning the train would have to slow down or even stop mid-journey, so the pressure sensor’s reliability is of paramount importance. Druck’s customer required the sensors to be highly accurate, stable and reliable in these harsh environments with a long service life. First-class quality control during production of the pressure sensors, fast local response from Druck’s China-based team pre and post sales were also a must for the customer.
Due to Druck’s in-depth understanding of the customer’s application and the long-term technical and commercial collaboration with them on this project, Druck have established a close partnership with the customer. After the introduction of Druck’s UNIK5000 pressure sensor and following extensive qualification and acceptance testing, the customer was very satisfied with UNIK5000’s high accuracy, reliability and long-term stability as well as Druck’s localised technical support, production and service capability.
A customised pressure connector was designed to further protect the pressure sensor from the damage of pressure shock. An M12*1 4pin electrical connector was chosen to make sure the sensor is IP65 dustproof and waterproof. QR codes were added to the sensors to help customer achieve digital production management. ESS (Environmental Stress Screening) test was also customised according to the customer’s requirements to ensure the quality of the product.
High precision and high stability of Druck’s UNIK5000 pressure sensors enable the customer to precisely control the train’s braking system to ensure that high-speed trains brake safely and smoothly. Considering the high volume of sensors used on the trains, the high reliability of the sensors that Druck have supplied allows the train operators to reduce their maintenance cost significantly.
Furthermore, localised production resulting in a short product lead time, excellent customisation capability, together with strong in-country technical support helped Druck’s customer seize this market opportunity and grow their business. This success for Druck demonstrates that the company’s global technical and service support footprint are as important as the first-class pressure sensor being supplied to the customer.
Find out more information about Druck on LinkedIn