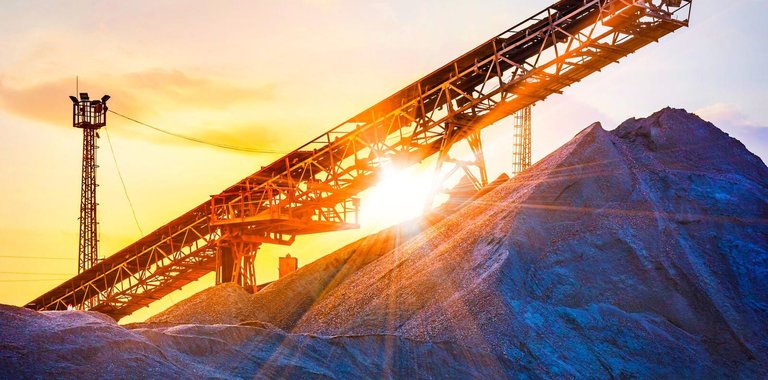
Digital Innovation in Mining Operations
As green energy needs spike, demand for minerals rises in-kind. Per a World Bank Group report, graphite, lithium, and cobalt production could increase by almost 500% by 2050 to meet the demands for clean energy. For mining companies around the world, this is welcome news. It is simultaneously an urgent call to action for miners to innovate operations.To meet the escalating demand for minerals, mining companies must proactively manage highly cyclical and capital-intensive operations by keeping the lowest possible production costs. By leveraging automation and digitally-savvy operations, miners can enable smarter, faster and safer decisions, resulting in greater productivity, improved safety and lower operating costs. Thus, it is digital innovation that will define the mines of the future.
As demand grows, process interruptions carry steeper costs. And, the primary root cause is the inefficiency of reactive maintenance approaches that impede a mine’s ability to fully capitalize on growing demand.
Specifically:
- 70% operating efficiency is the average, mostly due to breakdowns and stalled operations
- 30-50% of operating costs are spent on maintaining plant, fleet and equipment
- 3-5X more is spent on breakdowns and unplanned maintenance vs. planned maintenance
Thus, the first step in digital innovation is the adoption of condition monitoring systems to enable maintenance optimization and, in turn, improve operational efficiencies. Here are two application examples and outcomes, which showcase the transformative power of condition monitoring in mining operations.
In mining pump stations, pumps are responsible for 97% of unplanned maintenance costs. Pump reliability is crucial in the areas of safety, environmental impact, and efficient transportation. By monitoring key pump characteristics and employing real-time analysis of impending issues, mining operators enable early detection of issues before they occur. This averts lost revenue and reduces maintenance costs. In slurry pump applications, Bently Nevada uses dynamic pressure sensors to detect reciprocating diaphragm failures, providing a novel diagnostic to increase pump reliability, based on:
- The hydraulic fluid flexes the diaphragm
- When the diaphragm flexes, slurry is discharged
- Abrasive, corrosive slurries prohibit pressure sensor installations in slurry valves
- Thus, dynamic pressure monitoring of the hydraulic fluid assesses slurry discharge effectiveness
The result? A savings of US $3 million per year, based on maintenance cost recovery and capacity increases for a 10-pump station.
Consider this PwC mining example, where proactive maintenance enabled a 14% reduction in maintenance spend by mitigating unplanned downtime. This approach delivered US $8 million savings in operating expense (OpEx).
In order to reduce unplanned downtime, a condition monitoring system was designed and implemented on critical mining equipment. The insights provided by the smart sensors and algorithms alerts operators of potential failures. Repairs are scheduled proactively and coincide with planned maintenance, partial outage periods or normal equipment rotations. As a result, asset availability and reliability increase, production interruptions are minimized and maintenance costs are reduced.
The result? A 14% reduction in maintenance spend generates US $8 million in OpEx
Many other condition monitoring applications, such as wireless sensors for hoist systems and continuous monitoring for SAG (semi-autogenous grinding) mills are delivering transformational outcomes such as the two referenced above. The ultimate payoff will occur when these systems scale to be interconnected and provide an operation-wide, eagle’s eye view of an entire mine, thus enabling holistically optimized production.
Minerals are needed to fuel a greener future. Mining companies must better optimize production today to enable meeting this increasing demand. The first step in that optimization is condition monitoring to overcome existing maintenance inefficiencies and mitigate unplanned – and costly –downtime. In mining operations, green energy initiatives are catalyzed as production efficiency improves, delivering a promising future for mining companies, and humankind.
Want to learn more?
Speak with an SME today to get started on building a stronger future for your mining operations.