On a wind-whipped oil-producing steel island half an hour’s helicopter ride off the coast of Norway, a quiet industrial revolution has taken place. Automation and a timely tender have enabled the redistribution of tasks carried out offshore and onshore on Equinor’s Askepott rig, paving the way for decreased costs of oil production, improved working conditions for employees and the icing on the frosty cake — shavings in CO2 emissions.
The story of automation is becoming universal, but in industries ranging from financial and legal services to resource extraction it can typically replace only parts of individual roles. Managers globally are struggling to rearrange their workforces to enable efficiencies without losing people who have years of industry knowledge to contribute to future growth and innovation. In oilfield services, as machine learning is applied to tasks such as directional drilling, employees with industry experience will be essential to delivering on a forecast near-term increase in demand for oil.
Irene Hamre, Global Service Delivery Leader of Integrated Well Services at Baker Hughes, says the opportunity to throw all the tasks performed offshore into the air and rearrange them for a resilient future came when Equinor put up a tender designed to do just that.
“In the past, Equinor would have put up discreet tenders, so each rig might have had 10 different contracts for different services,” she says, with service providers likely being awarded different aspects and their employees working side by side in long-established roles on each rig. After some years of collaborating with suppliers on a model that would better integrate services and technologies, Equinor’s late-2017 tender called for a main service provider to deliver all the services for each rig or offshore asset.
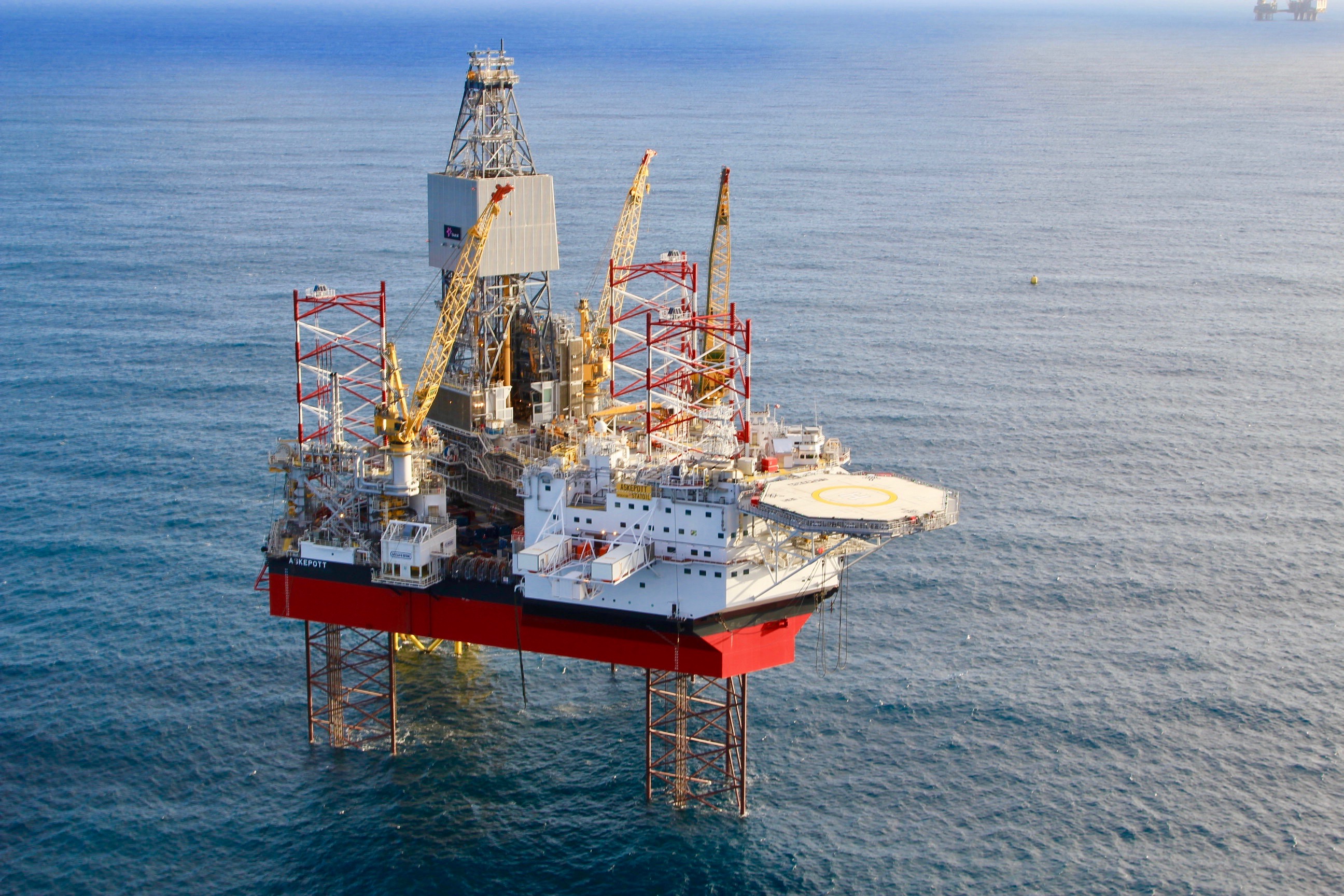
Bringing workers home
One of the main goals was to reduce the number of oilfield services crew working offshore on each rig by around 50% — a level of personnel that has become known as Integrated Operations Level 3 (IO Level 3).
Baker Hughes had led the industry over the years in its collaboration with Equinor, formerly known as Statoil (the company changed its name in May 2018 to mark its transition from purely oil-and-gas-based operations to a broader portfolio of energy generation that includes renewables) to unleash the human and technological potential of rig expertise from its decades-old inflexible structure. Strategically planned and implemented, the relocation of significant numbers of personnel onshore has the effect of better utilizing workforce skills, minimizing employee exposure to health, safety and environmental (HSE) risks; and reducing costs and logistics involved in well construction.
The tender, says Hamre, “was the real push for us not just to model various changes, but to initiate and prove them to the level Equinor had specified.”
The Askepott rig would become the testing ground for these changes, transforming roles involved in upstream drilling, multiskilling employees who would remain offshore, and bringing some new roles into a Remote Operations Center in Stavanger. This city of some 130,000 people is a microcosm of Norway’s heritage, economy and culture: home to the 13th Century Domkirke cathedral, the Norwegian Petroleum Museum, the Norwegian Canning Museum (think fish), it is also a departure point for cruises to Norway’s pristinely beautiful Lysefjord and adventure tourism in the region.
A large percentage of the offshore drilling workforce already live in or near Stavanger. One logistical challenge to implementing IO Level 3 was that the balance of employees have for years been flown in to Bergen or Stavanger from other remote, urban or international locations to then make the chopper hop to offshore rigs. To ensure the universal appeal to the workforce of transitioning opportunities, Baker Hughes arranged accommodation for them in Stavanger, to enable them to fulfil their new roles. The expectation is that within two to four years these employees will either move to Stavanger or become responsible for their own accommodation in the city during their shifts.
Among the greater challenges to redistributing tasks was satisfying experienced directional drillers who would now operate from onshore that digital connectivity could provide real-time responsiveness; satisfying regulatory authorities that risks and mitigations had been more than adequately balanced; and proving to unions that safety had been ensured to the highest standard.
“The latency of the data is very, very important and the security of the connection is vital,” says Chris Jones, Baker Hughes’ Vice President of Oilfield Services in Europe. “But on the rig, much of the drilling control is carried out from a 40-foot container that’s probably 100 feet from the drill floor — we’re not actually touching much anyway — so to be 100 miles away rather than 100 feet away is not that difficult as long as the connectivity is there.”
Where directional drillers were involved in physical tasks, says Jones, these have been “unentwined” from their roles and reallocated: “Making up drilling assemblies, plugging into tools, loading nuclear sources and managing drilling fluids are among the tasks that must remain on the rig.”
After rigorous testing, Equinor, Baker Hughes and rig contractor KCA Deutag in October 2019 celebrated successful transition of Askepott rig to new cross-skilled roles offshore, and roles such as directional drilling and advanced real-time engineering roles being carried out remotely from the onshore Remote Operations Centre in Stavanger. This cleared the way for a further 10 rigs to transition to IO Level 3 by mid-2020. Some 400 oilfield-services employees are undergoing training in roles revised to make the most of their time on rig, or to ensure their proficiency in remote operations.
A new tools specialist at work: It’s no picnic, but ...
The aggregation of hands-on drilling tasks that must be carried out offshore has meant that tools specialists like Andrew Gofas are much more consistently applying their skills and have a more predictable work schedule than previously. Gofas says that before IO Level 3 was introduced, he worked irregular stints on the rigs; as a measurement-while-drilling engineer, supporting drilling operations, he might be offshore for three to five days while a well section was being drilled, back home in Oslo for a few days, recalled to work when the next section was ready to be drilled and so on.
“Sometimes we might only be there for a day,” says Gofas.
With the reallocation of tasks enabled by one contractor — in this case Baker Hughes — controlling drilling-related operations for Askepott, Gofas has since been trained in numerous other competencies. They include spooling and banding of power cables, pressure integration, fuel gas systems management, liner-hanger work, and the use of wireline — cabling technology used to lift and lower equipment and measuring devices in and out of the well as required.
“Now, no matter what operation is going on, we’re involved,” says Gofas, who relishes being “much more occupied than we were before”. The upshot he says is that, “Now you’re 99.9% guaranteed a two-week hitch followed by four weeks off; I know when I’m going offshore and I know when I’m coming onshore — I can plan my life for the year.”
Gofas is among those employees who enjoys working offshore, no matter the conditions of weather and isolation. He says the dark, winter shifts of endless rain, snow or blizzard with constant 24-knot winds provide context and the means to enjoy his four weeks off, when he appreciates the contrast of “no fixed demands, no alarms set … and nice weather” as he travels the world.
With an electrical engineering degree from Arizona State University, Gofas joined Baker Hughes at its Houston headquarters in 2012, with the intention of climbing the company ladder. As part of that career path he was required to navigate a couple of years on the metal gangways and in the compact accommodation of offshore oil platforms — to develop his understanding of the business. On his first offshore hitch in 2013, he says he became hooked on the challenges, and knew he would never return to an R&D lab or an office.
Gofas says his 12-hour shifts are now much busier: “It’s a lot, but it’s not a lot at one time. It’s always one operation at a time. We’re learning a broader range of competencies, and my knowledge and experience as a tools specialist will be worth more — I like learning as much as I can.”
Reactions to the changes are of course individual, and not everyone feels as welcoming of IO Level 3 as Gofas. Jones, who was once an offshore directional driller, and who did return to shore years ago to undertake the different, hard-yards rise to VP, says, “Our people are on a journey with this, from grief, denial and anger, to acceptance, excitement and the whole gamut. We’re getting to a more positive place,” in adapting to the digital future of oil and gas.
Fueling future-focused economies — a world in transition
To Equinor, the transition means ongoing commercial viability for its offshore assets, says Jones: “It’s fundamental to Equinor to ensure that the Norwegian Continental Shelf stays relevant and competitive.”
Although Norway itself is almost completely powered by hydroelectricity, the oil and gas industry is significant to its economy, and world demand for oil — even as all global economies face the imperative to decarbonise — is set to increase for the coming 10 years, predict analysts at Rystad Energy. Head of the Rystad’s Oilfield Services Research, Audun Martinsen, says, “At Rystad we think oil production will need to grow towards 2028-29, from 99 million barrels per day of oil and liquid production, to around 107 million bpd, before demand starts to come down as passenger vehicles turn more towards electrically driven units.”
Automation and digitalisation of oil fields is “a key part of keeping those barrels economic”, says Martinsen. In October 2019 a study by Rystad Energy found that the oil industry could reduce its overall costs by as much as $100 billion through digitalisation and automation of processes.
At this stage of the transition to automation, savings will come from less obvious sources than reduced workforce headcount. Of 400 employees involved in the IO3 reallocation of tasks, Jones says there will be some efficiency gains in terms of a very small percentage of roles, but he envisages that these employees’ industry experience will be applied “elsewhere in the business where they’ll create more value for our customers and for Baker Hughes”.
However, reduced numbers of employees on the rigs he says, reduces the required size of offshore operations. Every 10 people accommodated and working offshore for example, requires an extra steward and an extra chef. Essentially, Jones says, “more people on a rig begets more people on a rig”, the structures themselves grow as a result, and helicopter flights proliferate. The cost of supporting an employee onshore is a fraction of funding their offshore deployment.
Automation also delivers more predictable and consistent outcomes. An automated drill, programmed and monitored by an experienced driller, says Jones, delivers a more consistent result in a shorter timeframe than the naturally varied output of human drill operators. The best directional driller may be able to outperform an AI-enabled automated system, but, Jones says, “The machine will consistently outperform the best directional driller having an average day.”
Martinsen says Rystad research confirms that automation can reduce the time taken to drill a well from 30 days to 20. The savings are in the repeatable, reliable nature of that outcome, and the ability to deploy the drilling asset more efficiently, with less downtime due to mistakes and the need to correct.
Embracing social responsibility
For workers, companies and unions, the impetus to bring employees onshore is also driven by health and safety considerations. “You are less likely to injure yourself in the remote operations center than you are on the rig,” says Jones, and risks and emergencies onshore are much easier to manage than those in remote locations where specialized medical assistance, for example, can be 30 to 90 minutes away by helicopter.
Emissions reductions that accrue from deploying smaller rigs, running fewer helicopter flights, and more efficiently using emissions-intense machinery may not be on the same scale as those achieved by carbon capture utilization and storage — reducing flaring of fugitive gas from oil wells by capturing and harnessing it to drive electricity-generating turbines. But they are among the incremental cuts to emissions that the industry is implementing to support its social license to operate.
Baker Hughes envisages that first-mover implementation of IO Level 3 at Equinor’s Norwegian operations, will ultimately improve the viability and sustainability of offshore rigs worldwide. Hamre is working on adapting the model to operations in Saudi Arabia and Mexico. Training and retraining of the workforce will become a fact of industry life.
Although there have been many challenges to implementing IO Level 3, the proof of concept at Askepott has helped build the metaphorical bridge to shore: “It’s been a positive experience,” says Hamre. “People were concerned that they wouldn’t feel as connected to the rig as they did offshore. In fact, the equipment is easy to manage and there’s reliable connectivity.” Plus, she says, “They get to go home to their families after each shift.”
Hamre concedes that as an architect and enabler of integrated well services “I’m kind of biased to the whole integrated future”. But, she says, the learnings emerging from reimagining roles on and offshore “are massive”. She says Baker Hughes employees will be released from siloed roles to become more knowledgeable across product lines and develop a more holistic view of operations and the industry.
“There are so many opportunities for employees and for us as a company to build on that context,” says Hamre, “to become more efficient and also have happier employees engaged in delivering better performance to our customers”.
Join former offshore directional driller Nils-Tore Jorddal in the Remote Operations Center for an insight into his new onshore role as a Well-Placement Engineer, in which he’s working with peers to hone Baker Hughes drilling services ... and going home for dinner each evening.
Energy Forward Stories
Sign up to stay up to date on the latest innovations and people shaping the future of our industry.